In the manufacturing sector, where efficiency and productivity are paramount, effective Integrated Facility Management services emerge as a critical component for achieving and maintaining optimal operations. These professionals serve as the backbone of manufacturing operations, ensuring that the physical infrastructure and support services necessary for production are expertly managed and maintained. From equipment upkeep to safety compliance, their responsibilities encompass a broad spectrum of tasks that are vital for the smooth functioning of manufacturing facilities. From ensuring machinery uptime to optimizing workflows, facility management in manufacturing facilities plays a pivotal role in enhancing Return on Investment (ROI) and overall business success. By leveraging Integrated Facility Management services, manufacturing clients can unlock numerous benefits that directly contribute to enhance ROI.
In this blog, we explore five key advantages of facility management tailored specifically to manufacturing environments, explaining how they can significantly boost ROI.
1. Streamlined Operations and Maintenance:
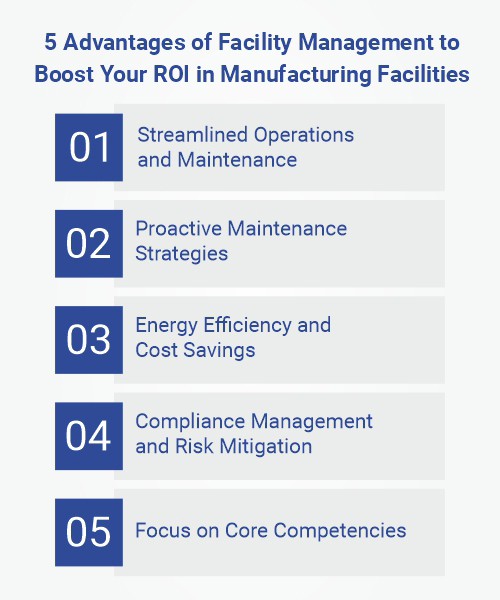
Integrated Facility Management service providers offer a holistic approach to managing manufacturing facilities by consolidating various services under one umbrella. By integrating maintenance, cleaning, security, and other essential functions, IFM providers streamline operations and ensure seamless coordination between different service teams. This integration eliminates redundancies, minimizes downtime, and enhances overall operational efficiency. With optimized operations, manufacturing clients can increase productivity, reduce production bottlenecks, and ultimately improve ROI by maximizing output with minimal resources.
2. Proactive Maintenance Strategies:
In manufacturing facilities, machinery downtime can have a significant impact on production schedules and ultimately on the bottom line. Effective maintenance is critical for ensuring the reliability and longevity of manufacturing equipment. IFM service providers employ proactive maintenance strategies, such as predictive maintenance and condition monitoring, to identify potential issues before they escalate into costly breakdowns. By leveraging data analytics and IoT-enabled sensors, IFM providers can detect equipment anomalies, assess performance trends, and schedule maintenance activities accordingly. By minimizing unplanned downtime and reducing maintenance costs, proactive maintenance strategies directly contribute to improving ROI for manufacturing clients.
3. Energy Efficiency and Cost Savings:
Manufacturing facilities are often energy-intensive environments, leading to substantial utility expenses. IFM providers specialize in implementing energy-efficient solutions and sustainability initiatives to reduce energy consumption and lower operating costs. Through measures such as upgrading energy-saving lighting systems, optimizing HVAC controls, and implementing renewable energy technologies, IFM providers help manufacturing clients achieve significant cost savings while minimizing their environmental footprint. By optimizing energy usage and reducing utility expenses, IFM services directly contribute to improving ROI for manufacturing facilities.
4. Compliance Management and Risk Mitigation:
Manufacturing facilities are subject to a myriad of regulatory requirements related to health, safety, environmental protection, and labour practices. Non-compliance with these regulations can result in fines, penalties, and reputational damage. Integrated Facility Management service providers assist manufacturing clients in navigating complex regulatory landscapes by ensuring compliance with relevant laws and standards. From conducting safety audits to implementing training programs, IFM providers help mitigate risks associated with regulatory non-compliance, thereby safeguarding the continuity of operations and preserving ROI for manufacturing clients.
5. Focus on Core Competencies:
By outsourcing facility management services to IFM providers, manufacturing clients can free up valuable resources and focus on their core competencies. Instead of allocating time and manpower to non-core activities such as maintenance, cleaning, and security, manufacturing clients can entrust these responsibilities to IFM experts. This allows them to concentrate on innovation, product development, and market expansion initiatives that drive revenue growth and enhance competitive advantage. By optimizing resource allocation and enhancing operational focus, IFM services enable manufacturing clients to achieve higher ROI and long-term sustainability.
In conclusion
At FFS, our Integrated Facility Management Services offers a myriad of benefits for manufacturing clients seeking to enhance ROI and operational efficiency. By streamlining operations, implementing proactive maintenance strategies, optimizing energy usage, ensuring regulatory compliance, and enabling focus on core competencies, FFS has been playing a crucial role in maximizing the value proposition for manufacturing facilities. Investing in IFM services is not only a strategic decision but also a pathway to achieving sustained growth, profitability, and competitive advantage in today's dynamic manufacturing landscape.
Visit our Integrated Facility Management section now to get a free quote today to enhance the ROI and operational efficiency of your manufacturing facility.
Industries we serve:
Automobile | Ancillary | Manufacturing | Pharmaceutical | healthcare | Oil and Gas | FMCG | Education | Real Estate | Commercial
Outsourcing IFM services can provide specialized expertise, cost-effectiveness, access to advanced technology, scalability, and the ability to focus on core business activities while experts manage facility operations.
Key performance indicators (KPIs) such as uptime of critical equipment, energy efficiency, maintenance costs, safety records, compliance levels, and overall productivity are often used to measure the success of IFM practices.
Trends like the Internet of Things (IoT) integration, artificial intelligence for predictive maintenance, sustainable practices, remote monitoring and management, and the adoption of cloud-based solutions are shaping the future landscape of IFM.
Soft services encompass a range of human-centered services aimed at creating a comfortable, secure environment. These services primarily involve human interaction and contribute to enhancing the overall ambience. Examples include housekeeping, payroll management, pest control, front office management, pantry services, front desk support, and landscaping.