Introduction :
Energy management is crucial in facilities management services in India due to its significant impact on operational costs, environmental sustainability, and overall efficiency. Effective energy management helps facilities reduce energy consumption, leading to substantial cost savings and improved profitability. Additionally, it supports environmental goals by lowering greenhouse gas emissions and reducing the facility's carbon footprint. By implementing energy-efficient practices and technologies, facilities can enhance their operational performance, ensure regulatory compliance, and contribute to broader sustainability initiatives. Moreover, energy management fosters a culture of conservation and awareness among employees, promoting long-term behavioural changes that further drive efficiency and sustainability. This blog explores various strategies that can help facilities in India manage energy efficiently and sustainably.
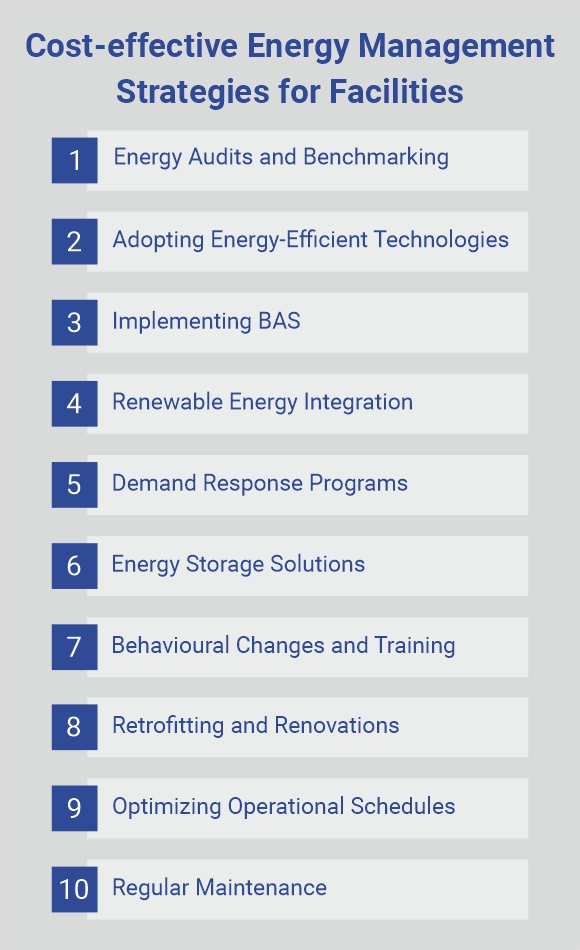
1. Energy Audits and Benchmarking
The first step in effective energy management is understanding current energy consumption patterns. Conducting comprehensive energy audits helps identify areas of inefficiency and potential savings. Benchmarking energy usage against industry standards or similar facilities provides a clear picture of where improvements can be made.
Steps to Implement:
- Hire a certified energy auditor to assess your facility.
- Use energy management software to track and analyze energy consumption.
- Compare your energy usage data with industry benchmarks
2. Adopting Energy-Efficient Technologies
Investing in energy-efficient technologies can yield significant long-term savings. Upgrading to energy-efficient lighting, HVAC systems, and machinery can reduce energy consumption and costs.
Key Technologies:
- LED Lighting: Replace traditional incandescent and fluorescent bulbs with LED lights, which consume less energy and have a longer lifespan.
- High-Efficiency HVAC Systems: Upgrade to HVAC systems with higher SEER (Seasonal Energy Efficiency Ratio) ratings to improve energy efficiency.
- Variable Frequency Drives (VFDs): Install VFDs on motors and pumps to adjust their speed based on demand, reducing energy wastage.
3. Implementing Building Automation Systems (BAS)
Building Automation Systems (BAS) allow for centralized control of a facility's heating, cooling, lighting, and other systems. BAS can optimize energy usage by automating system operations based on occupancy, time of day, and environmental conditions.
Benefits of BAS:
- Energy Savings: Automate lighting and HVAC to operate only when needed.
- Improved Comfort: Maintain optimal indoor conditions for occupants.
- Remote Monitoring: Enable remote monitoring and control, allowing for quick adjustments and troubleshooting.
4. Renewable Energy Integration
Integrating renewable energy sources such as solar, wind, and biomass into facility operations can reduce dependence on conventional energy sources and lower energy costs.
Renewable Energy Options:
- Solar Panels: Install solar panels on rooftops or open spaces to generate electricity on-site.
- Wind Turbines: Use wind turbines in areas with adequate wind resources.
- Biomass Boilers: Utilize biomass boilers for heating applications, particularly in regions with abundant biomass resources.
5. Demand Response Programs
Participating in demand response programs can help facilities manage energy costs by reducing or shifting energy usage during peak demand periods. These programs often provide financial incentives for facilities that lower their energy consumption during critical times.
How to Participate:
- Enroll in demand response programs offered by utility companies or third-party aggregators.
- Identify non-essential loads that can be curtailed or shifted during peak demand periods.
- Implement automated controls to respond to demand response signals.
6. Energy Storage Solutions
Energy storage solutions, such as batteries, can store excess energy generated during off-peak periods for use during peak demand times. This helps in balancing energy supply and demand, reducing peak energy charges, and enhancing energy reliability.
Types of Energy Storage:
- Lithium-Ion Batteries: Commonly used for their high energy density and efficiency.
- Thermal Storage: Stores energy in the form of heat or cold for later use in heating or cooling applications.
- Pumped Hydro Storage: Uses excess electricity to pump water uphill to a reservoir, which is then released to generate electricity during peak periods.
7. Behavioural Changes and Training
Promoting energy-conscious behaviour among employees and providing training on energy management can lead to significant energy savings. Employees play a critical role in the overall energy consumption of a facility.
Strategies to Encourage Behavioral Changes:
- Conduct regular training sessions on energy conservation practices.
- Implement an energy awareness campaign to highlight the importance of energy savings.
- Encourage employees to switch off lights, computers, and equipment when not in use.
8. Retrofitting and Renovations
Retrofitting existing facilities with energy-efficient upgrades and renovations can drastically reduce energy consumption. This includes improving insulation, sealing leaks, and upgrading windows and doors.
Retrofitting Measures:
- Insulation: Improve insulation in walls, roofs, and floors to reduce heat loss in winter and heat gain in summer.
- Window Upgrades: Install energy-efficient windows with low-emissivity (low-E) coatings to minimize heat transfer.
- Sealing Leaks: Seal gaps and cracks around doors, windows, and other openings to prevent air leakage.
9. Optimizing Operational Schedules
Optimizing the operational schedules of energy-intensive equipment can lead to substantial energy savings. This involves running equipment during off-peak hours when energy rates are lower and avoiding the simultaneous operation of multiple high-energy-consuming devices.
Steps to Optimize Schedules:
- Analyze energy usage patterns to identify peak and off-peak periods.
- Schedule energy-intensive operations during off-peak hours.
- Use timers and programmable controls to automate the scheduling process.
10. Regular Maintenance
Regular maintenance of equipment and systems ensures they operate efficiently and consume less energy. This includes cleaning, lubricating, and tuning up machinery and systems to prevent energy wastage due to wear and tear.
Maintenance Best Practices:
- Develop a preventive maintenance schedule for all equipment.
- Conduct routine inspections to identify and address issues promptly.
- Replace worn-out components to maintain optimal performance.
Conclusion
Cost-effective energy management strategies are essential for facilities in India to reduce energy consumption, lower costs, and minimize environmental impact. By conducting energy audits, adopting energy-efficient technologies, implementing BAS, integrating renewable energy, participating in demand response programs, utilizing energy storage solutions, encouraging behavioural changes, retrofitting facilities, optimizing operational schedules, and maintaining equipment regularly, facilities can achieve significant energy savings. As India continues to develop and urbanize, these strategies will play a crucial role in ensuring sustainable and efficient energy use in facilities management.
Unlock the full potential of your facility with our customized facility management services. Reach out to us today to take the first step towards optimized efficiency.
Industries we serve:
Automobile | Manufacturing | Pharmaceutical | Oil and Gas | Healthcare | Ancillary | FMCG | Education | Real Estate | Commercial | Mining | Hotels
Also read: The Importance of Regular Facility Maintenance in Facility Management