In today's hyper-competitive business environment, organizations are constantly seeking ways to streamline operations and reduce costs while enhancing productivity and service quality. One of the most effective strategies to achieve these objectives is through Integrated Facility Management (IFM). At its core, IFM consolidates multiple facility services under a single management structure to achieve cost efficiency, better resource utilization, and improved operational performance.
Among the many benefits of IFM, cost management stands out as a critical advantage. Effective cost management involves strategic budgeting, robust financial planning, and the ability to identify areas where expenses can be minimized without compromising service quality or employee satisfaction. This blog delves into the importance of cost management within IFM, explores key budgeting and financial planning strategies, and outlines how IFM can significantly reduce operational costs.
Understanding Integrated Facility Management (IFM)
Integrated Facility Management is the practice of consolidating all facility-related services—such as housekeeping, maintenance, security, food services, landscaping, pest control, and more—under a unified management system. Rather than dealing with multiple vendors for each service, organizations partner with a single IFM provider to manage the full spectrum of facility needs. This integration not only simplifies vendor relationships but also brings in centralized planning, real-time monitoring, standardized procedures, and data-driven decision-making, all of which contribute to improved financial efficiency.
The Significance of Cost Management in IFM
Cost management is a fundamental element of IFM, especially in sectors such as manufacturing, healthcare, education, IT, and logistics, where facility operations can constitute a substantial portion of overall operational costs.
Effective cost management through IFM includes:
- Reducing redundant services and streamlining operations
- Utilizing technology for monitoring and automation
- Planning and allocating budgets more strategically
- Lowering total cost of ownership through long-term asset management
- Enhancing productivity and reducing downtime
With these advantages, cost management becomes a driving force behind the decision to adopt IFM.
Budgeting and Financial Planning in IFM
1. Strategic Budgeting:
An integrated approach allows for holistic budgeting rather than fragmented allocations across departments or service lines. Strategic budgeting in IFM involves:
- Forecasting operational needs: Based on historical data and predictive analytics.
- Setting service priorities: Determining which services are critical and aligning budget accordingly.
- Allocating resources smartly: Preventing over-expenditure in non-critical areas and ensuring high-priority areas are adequately funded.
For example, an organization may decide to automate routine housekeeping tasks using robotic machines and allocate human resources to more complex activities, optimizing labor costs without sacrificing cleanliness or hygiene.
2. Lifecycle Costing:
Lifecycle costing is a budgeting method that considers the total cost of ownership (TCO) of assets—right from acquisition to maintenance to disposal. IFM providers often use lifecycle costing to recommend cost-efficient asset investments and preventive maintenance schedules, thus reducing the likelihood of expensive emergency repairs or premature replacements.
3. Financial Planning for Capital Improvements:
IFM providers also play a pivotal role in long-term financial planning by advising on capital improvements. This might include infrastructure upgrades, energy efficiency initiatives, or renovation plans, with clear cost-benefit analyses and ROI calculations to help organizations make informed financial decisions.
4. Variance Analysis and Cost Tracking
Regular monitoring of actual vs. budgeted expenses allows facility management service provider to adjust plans in real-time and identify any inefficiencies. Variance analysis helps pinpoint over-expenditure trends and make corrective decisions before costs spiral out of control.
Reducing Operational Costs through IFM
One of the most compelling benefits of IFM is its ability to significantly reduce operational costs while maintaining or even improving the quality of services.
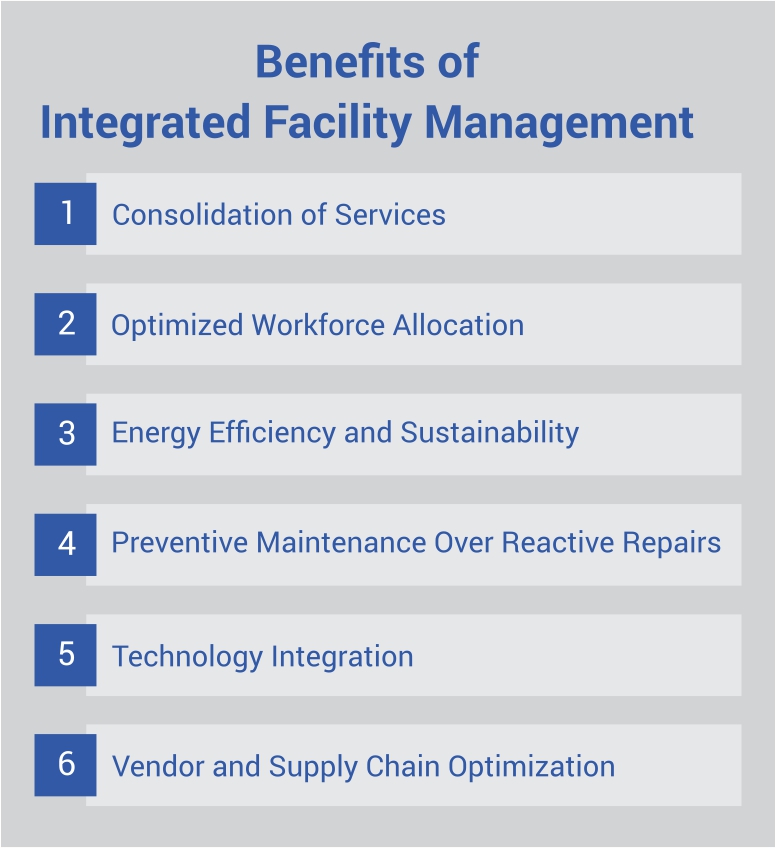
1. Consolidation of Services:
Rather than managing multiple vendors for maintenance, cleaning, landscaping, and catering, IFM combines them under one provider. This leads to:
- Reduced administrative overheads
- Lower contract management costs
- Economies of scale on procurement
- Standardized service delivery
2. Optimized Workforce Allocation:
With IFM, staff can be cross-trained to handle multiple tasks, which minimizes idle time and maximizes productivity. For instance, during low-traffic hours, housekeeping staff might be reassigned to pantry duties or basic maintenance support, reducing the need for dedicated personnel for each function.
3. Energy Efficiency and Sustainability:
A good IFM provider integrates energy management strategies as part of their offering. This can involve:
- Installation of smart meters
- LED lighting upgrades
- HVAC system optimization
- Waste reduction programs
These initiatives, while improving environmental sustainability, also lead to tangible cost savings in utility bills and resource consumption.
4. Preventive Maintenance Over Reactive Repairs:
Preventive and predictive maintenance is far more cost-effective than reactive maintenance. IFM teams ensure that:
- Equipment is regularly inspected and maintained
- Asset downtime is minimized
- Costly breakdowns are prevented
This shift from reactive to proactive maintenance greatly improves asset longevity and reduces long-term expenses.
5. Technology Integration:
The adoption of Facility Management Software, IoT-enabled devices, CMMS (Computerized Maintenance Management Systems), and data analytics enables:
- Real-time monitoring of operations
- Automated scheduling of tasks
- Performance tracking of assets and personnel
- Cost-saving insights and data-backed decision-making
This use of technology transforms the traditional approach into a leaner, more efficient operational model.
6. Vendor and Supply Chain Optimization:
IFM providers often have established relationships with vendors and suppliers, allowing them to procure materials, equipment, and services at discounted rates. Bulk purchasing, standardized specifications, and centralized procurement result in lower supply chain costs.
Case Study Example: Manufacturing Facility Adopting IFM
Consider a large manufacturing unit that used to manage 10 different service providers for various facility needs—from cleaning to catering. The administrative burden was high, and operational costs were rising with no central accountability.
After transitioning to an IFM model, the company achieved:
- 20% reduction in facility operating costs
- Improved service delivery times
- Standardized performance metrics
- Energy cost savings through automated systems
- Better financial visibility with a consolidated budget
This transformation clearly showcases how IFM serves as a strategic tool for cost management.
Measuring the Impact: KPIs for Cost Management in IFM
Organizations can monitor the success of cost management initiatives in IFM through key performance indicators such as:
- Cost per square foot of facility operation
- Reduction in utility bills
- Maintenance cost per asset
- Service-level compliance rate
- Energy consumption per unit of output
- Employee satisfaction scores (as a result of cleaner, better-managed facilities)
By aligning these KPIs with business objectives, companies ensure that their IFM model remains both cost-effective and performance-oriented.
Why Partner with a Professional IFM Provider?
Not all IFM providers are created equal. A professional IFM partner brings:
- Industry expertise across multiple sectors
- Access to latest tools and technologies
- Centralized command centers and dashboards for real-time visibility
- Trained workforce capable of cross-functional tasks
- Customized financial planning for facility operations
This makes them an indispensable ally in the journey toward cost-efficient, high-performing workplaces.
Conclusion:
In a world where operational efficiency is not just an advantage but a necessity, cost management through Integrated Facility Management in India has emerged as a game-changer. It goes beyond mere cost-cutting—it is about smart allocation of resources, future-ready planning, automation, and creating synergy across service lines.
By implementing robust budgeting and financial planning mechanisms, and leveraging the cost-reduction capabilities of IFM, organizations can unlock significant value - not just in savings, but also in service quality, employee satisfaction, and long-term sustainability.
If you’re looking to optimize your facility and management operations while keeping your budget in check, it's time to explore the power of Integrated Facility Management.
Industries we serve:
Automobile | Ancillary | Manufacturing | Pharmaceutical | Healthcare | Oil and Gas | FMCG | Education | Real Estate | Commercial
Also read: Measuring the ROI of Integrated Facility Management