Explore how predictive maintenance is revolutionizing maintenance and operations in India, significantly boosting asset lifespan and minimizing downtime. This blog highlights how a forward-thinking facility management service provider uses smart technologies to enhance performance and reduce costs. Learn why partnering with a top facility management service provider ensures reliable, long-term infrastructure health through innovative facilities and management practices tailored to India’s evolving industrial and commercial landscape.
How Predictive Maintenance Improves Asset Longevity in India
In a fast-evolving industrial and commercial environment like India, organizations face growing pressure to reduce downtime, optimize performance, and extend the life of their critical assets. One of the most transformative innovations reshaping maintenance and operations in India is predictive maintenance. With the help of data, sensors, analytics, and AI, predictive maintenance allows facility managers to monitor equipment health in real time and address issues before they lead to costly failures.
As India pushes forward with smart cities, large-scale infrastructure, and industrial automation, predictive maintenance is no longer a luxury-it's a necessity. For Facility Management Companies in India, this shift represents a golden opportunity to boost client satisfaction and cut costs through smarter, data-driven upkeep strategies.
This blog explores how predictive maintenance enhances asset longevity, its growing relevance in India, and why partnering with top facility management companies offering facility management solutions is key to success.
Understanding Predictive Maintenance
Predictive maintenance (PdM) is a proactive approach that uses advanced technologies, like IoT sensors, machine learning, and big data analytics—to detect anomalies and predict equipment failures before they occur.
Unlike preventive maintenance (which follows fixed schedules regardless of actual equipment condition), predictive maintenance is condition-based. It gathers real-time data from machines, vibration levels, temperature, fluid levels, voltage, etc.—and analyzes this data to forecast failures. This allows maintenance teams to act just in time rather than too late or too early.
Importance of Predictive Maintenance in the Indian Facility Management Sector
India’s facility management industry has witnessed exponential growth over the past decade. With sectors like manufacturing, pharmaceuticals, IT parks, real estate, and logistics rapidly expanding, the demand for efficient maintenance and operations in India is higher than ever. However, many of these industries face challenges like:
- Equipment downtime causing production losses
- Over-reliance on manual inspections
- Shortened asset life due to reactive or poorly timed maintenance
- Escalating operational costs due to equipment failures
Here’s where Facility Management Service Providers come into play. By integrating predictive maintenance into their service portfolios, these providers can offer Facility Management Solutions that deliver measurable value in terms of reduced breakdowns, longer asset life, and improved ROI.
How Predictive Maintenance Extends Asset Longevity
1. Early Fault Detection
Predictive maintenance tools continuously monitor the health of equipment. By detecting signs of wear and tear, misalignment, overheating, or imbalance early, maintenance teams can take action before a minor issue escalates into a major failure. This early intervention protects critical components, extending the asset’s usable life.
2. Reduced Wear from Over-Maintenance
Traditional time-based preventive maintenance often leads to over-maintenance—servicing equipment too frequently, sometimes even when it's not necessary. This over-servicing can wear down components, reducing their lifespan. PdM eliminates this problem by servicing assets only when they show signs of degradation.
3. Real-Time Condition Monitoring
Using IoT-enabled sensors, predictive systems gather real-time data that allows facility managers to track asset health continuously. This prevents blind spots in maintenance and ensures that equipment is operating within safe thresholds at all times—crucial for industrial environments in India where fluctuating power supply, temperature, and humidity can accelerate equipment wear.
4. Better Spare Part Utilization
Accurate predictions allow maintenance teams to plan ahead, ensuring that the right parts are available when needed. This reduces downtime and avoids emergency fixes that can involve makeshift or incorrect parts, thereby preserving the asset’s design integrity.
5. Customized Maintenance Strategies
Predictive maintenance helps in tailoring strategies based on how an asset actually performs under real-world conditions. This personalization ensures that each asset gets the exact care it needs-no more, no less—ultimately increasing its longevity.
Real-World Applications in Indian Context
Manufacturing Sector
In India’s booming manufacturing hubs-like Pune, Chennai, and Ahmedabad-predictive maintenance is playing a critical role in improving the reliability of machinery like CNC machines, chillers, boilers, and compressors. Top Facility Management Companies in India that serve these sectors are leveraging PdM to prevent costly halts in production lines, reduce scrap, and optimize equipment lifecycles.
Healthcare and Pharmaceuticals
Pharmaceutical plants and hospitals rely on high-performance HVAC systems, sterilizers, and diagnostic machines. Predictive maintenance ensures that critical equipment does not fail during operations, protecting both asset health and human life.
Commercial Real Estate and IT Parks
India’s urban centers are home to thousands of commercial buildings and IT parks that require 24/7 HVAC, electrical, and elevator systems. Predictive tools are now being adopted to ensure these assets run reliably and efficiently with minimal downtime and energy waste.
Infrastructure and Utilities
From water treatment plants to power stations, predictive maintenance is helping utility providers in India manage their aging infrastructure, avoiding catastrophic failures and costly shutdowns.
The Role of Facility Management Companies in India
As the industry moves from reactive to proactive and intelligent maintenance, Facility Management Companies in India are investing in new capabilities to offer smart facility management solutions. Here's how:
- IoT Integration: By installing smart sensors on HVAC units, pumps, escalators, and generators, FM companies can collect actionable data to drive maintenance planning.
- Analytics Platforms: Advanced dashboards help maintenance teams visualize trends and identify at-risk assets.
- Mobile Apps for Field Technicians: Real-time alerts and diagnostic tools empower technicians to address issues before they escalate.
- Centralized Maintenance Command Centers: Monitoring multiple sites across India to track asset health from a central location.
In doing so, these companies are no longer just service providers-they are strategic partners helping clients protect their infrastructure investments.
Benefits of Predictive Maintenance for Indian Facilities and Management
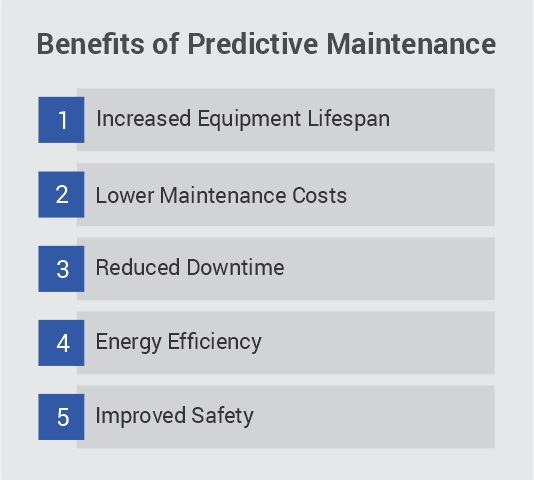
Increased Equipment Lifespan: Predictive maintenance dramatically extends the life of mechanical, electrical, and electronic systems by preventing failures that cause irreparable damage.
Lower Maintenance Costs: Data shows that predictive maintenance can reduce maintenance costs by 20–30% compared to reactive approaches. For clients in India who often work on tight budgets, this is a game-changer.
Reduced Downtime: PdM minimizes unexpected equipment breakdowns, ensuring continuous operations-vital for industries like FMCG, BPOs, and manufacturing.
Energy Efficiency: Healthy equipment runs more efficiently. Predictive maintenance helps maintain optimal performance, reducing energy consumption and environmental footprint-important in India’s push toward sustainability.
Improved Safety: Predicting and preventing equipment failure reduces the chances of accidents, thereby ensuring a safer work environment, a crucial factor under India’s growing compliance mandates.
Challenges and the Road Ahead
Despite its benefits, adoption of predictive maintenance in India still faces a few hurdles:
- High Initial Investment: The cost of sensors, software, and training can be a barrier for small and medium enterprises.
- Lack of Skilled Workforce: There’s a need for more trained technicians who can interpret sensor data and take appropriate action.
- Integration with Legacy Systems: Many Indian industries still operate on outdated equipment that isn’t sensor-compatible.
However, Facility Management Service Providers are bridging this gap by offering predictive maintenance as a scalable, managed service, reducing upfront costs for clients while delivering long-term savings and asset protection.
Why Choose a Top Facility Management Company?
If your organization is looking to implement predictive maintenance, collaborating with one of the top facility management companies in India is the ideal route. These firms already have the technological infrastructure, trained staff, and industry experience to:
- Deploy scalable predictive maintenance tools
- Customize maintenance protocols for your asset portfolio
- Offer real-time monitoring and analytics
- Optimize lifecycle cost of your equipment
Their end-to-end facilities and management services allow clients to focus on their core business while ensuring that their assets operate reliably and efficiently.
Conclusion
Predictive maintenance is revolutionizing maintenance and operations in India, helping organizations of all sizes protect their critical assets, reduce operational disruptions, and extend equipment lifespans. As India continues to industrialize and urbanize, the role of facility management solutions that integrate predictive technologies will only grow stronger.
For organizations seeking reliability, cost-efficiency, and future-readiness, aligning with a Facility Management Service Provider offering predictive maintenance is no longer optional-it’s strategic.
By choosing the top facility management companies in India, businesses can harness cutting-edge technology and skilled expertise to ensure that their assets remain robust, reliable, and long-lasting-today and into the future.
Industries we serve:
Automobile | Ancillary | Manufacturing | Pharmaceutical | Healthcare | Oil and Gas | FMCG | Education | Real Estate | Commercial
Also read: The Role of Facility Managers in Employee Retention