Facility management and safety go hand in hand. No matter the industry, safety management is a top priority in every workplace. Efficient safety management is an integral part of facility management as it helps to protect everyone from potential hazards. We at FFS, believe that safety is not just about ticking boxes but creating a healthy & safe workplace for all. Let's do our part in creating a safe workplace every day, not just during this week.
Here are some essential industrial safety tips to improve operations at industrial sites
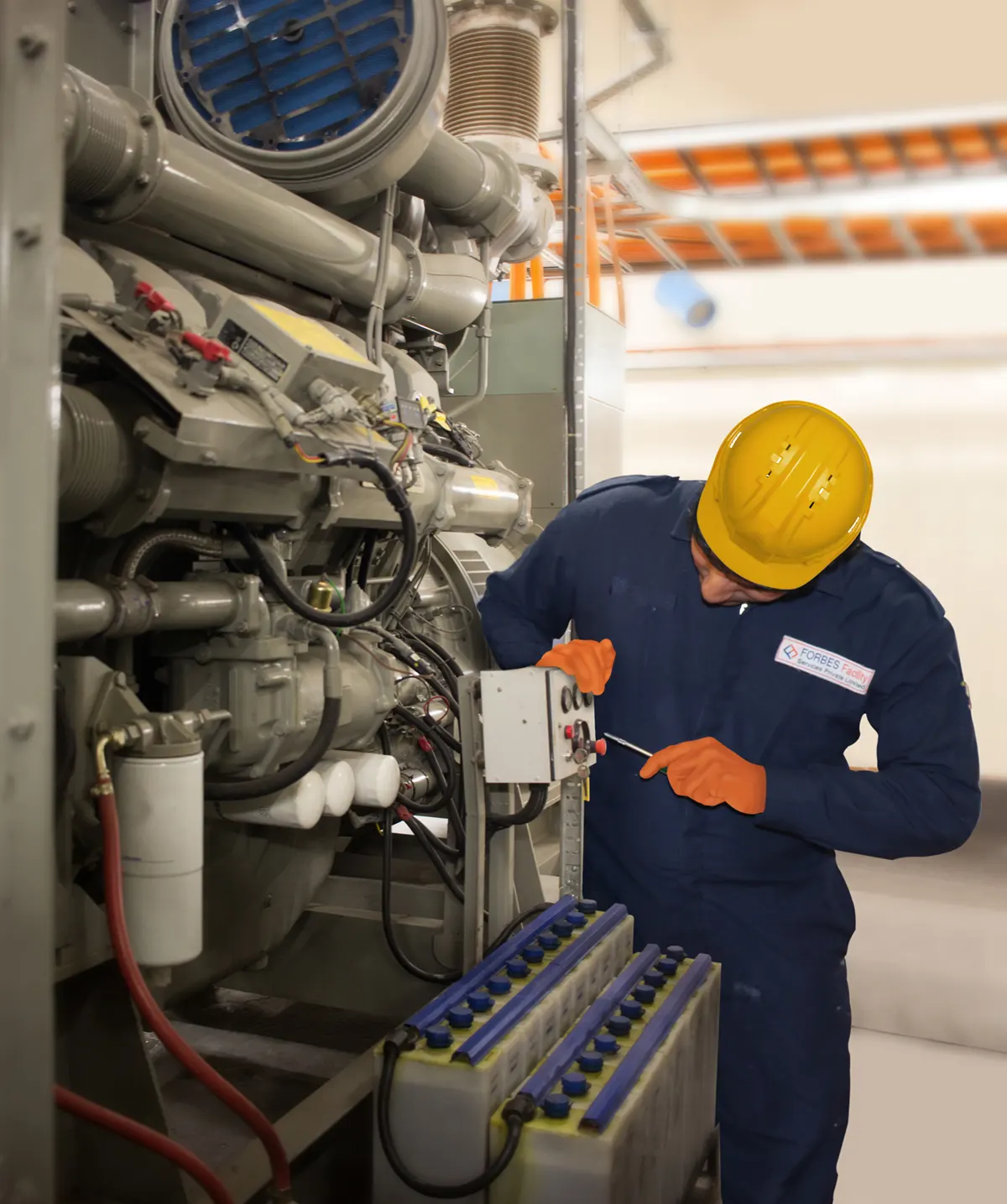
1. Safety Equipment
First and foremost safety gear is the most critical. All workers on site should wear the required safety gear at all times. The gear should be maintained, cleaned, and hygienic and staff should avoid sharing gear for 100% safety. We must ensure that all gear is as per the size and fit to avoid any gear malfunctions or mishaps. All staff should avoid wearing any form of loose clothing or jewellery while wearing the gear. Safety gear includes items such as PPE kits, hazard jackets, industrial caps, industrial boots etc.
2. Risk Assessment
Timely rounds of the facility to check and recheck that all equipment is in perfect working condition. To assess the risks around the facility like any hanging wires, damaged machinery or any such risks must be assessed continuously to prevent any mishaps at the site.
3. Preventive Maintenance
Preventive maintenance is a proactive activity wherein all machinery, equipment, electricals, HDAC etc. is checked thoroughly for any damages, oiling, maintenance, replacement of part etc. This activity is to ensure that we don’t wait for any calamity to take place and be proactive instead of reactive.
4. Training and Drills
Training at industrial plants is extremely essential, right from technical training to safety training. Every staff on site, whether they are handling equipment on a daily basis or not, should undertake basic machine training to be able to handle sudden accidental situations. Along with technical operation and maintenance training of the equipment, safety training should also be conducted for a basic understanding of switch on or off mode in emergency situations.
Safety training and mock drills should be conducted periodically for evacuation, fire fighting, first aid and any other emergencies. All staff must be aware of all emergency protocols - exits, safe spaces, alarms
5. Emergency Evacuation Drills
Fire and other evacuation drills are an excellent way to help everyone understand the best conduct in case of an emergency. Employees should be familiar with all emergency exists and know where fire extinguishers are kept and how to use them. It’s also important to determine which machines must be shut down and which can be left running while evacuating the building.
6. Working with Tools
All tools should be kept clean and in perfect working condition. Any defects should be immediately reported. Also, no tools should be left in a location not meant for storage.
7. Operating Heavy Machinery
Machinery should be in full working condition and have all the manufacturer’s safety guards installed. Anytime a malfunction or defect is noticed, go straight to the maintenance department and review the instruction manual. After your work is done, always remember to shut down the machine.
8. Maintaining Cleanliness
Keeping your work area clean does wonders when it comes to preventing accidents. A clean and organized area helps to create a better, less stressful work atmosphere. Many factors should be taken into consideration, including proper ventilation and lighting fixtures.
9. Prevent Slips and Trips
As the second most prevalent cause of nonfatal occupational injuries, it is vital to ensure that aisles are clear and spills are cleaned to prevent employees from tripping or slipping. If you are dealing with a liquid, use drip pans and guards. Clean up any spills immediately to keep conditions safe. Also, check your workplace to make sure there are no holes, loose boards, or nails projecting from the floor.
10. Prevent Objects from Falling
To keep objects from falling, use protections such as nets, toe boards, and toe rails. In addition, stack boxes straight up and down, and place heavy objects on lower shelves. Furthermore, keep stacked objects out of the way of aisles and work areas.
11. Eliminate Fire Hazards
If you are using combustible materials in the work environment, only keep the amount you need for the task at hand. When you are not using the flammable material, store the chemical in an assigned safe storage area away from sources of ignition. Also, store combustible waste in metal receptacles and dispose of it daily. How you dispose of chemicals and other fire hazards is also crucial for workplace safety.
12. Keep Emergency Exits Clear
Make sure to remove any clutter blocking emergency exits, equipment shutoffs, and areas where you are working. A cluttered work area can lead to not having enough space to use tools and pick up heavy objects properly. Furthermore, if an exit is obstructed, you may not be able to quickly escape if an emergency occurs. Placing equipment in proper storage areas after use will help keep the work area and emergency exits clear.
13. Conduct Frequent Safety Inspections and Audits
Casually strolling through the workplace doesn’t mean you are going to catch all of the potential safety violations. It’s something you actively need to look for. Scheduling routine safety inspections into your weekly calendar can help you spot anything that can be a potential hazard for employees.
Read More Five Key Steps to Create a Preventive Maintenance Schedule - FFS