Introduction :
The manufacturing industry is the backbone of economies worldwide, driving innovation, employment, and economic growth. Within this industry, facility management plays a crucial role in ensuring smooth operations, safety, and productivity. Regular maintenance is a key component of effective facility management, particularly in manufacturing, where equipment, machinery, and infrastructure are subject to rigorous use and wear. This blog explores the importance of regular Maintenance and Operations in facility management within the manufacturing industry, highlighting its benefits and the best practices for implementation.
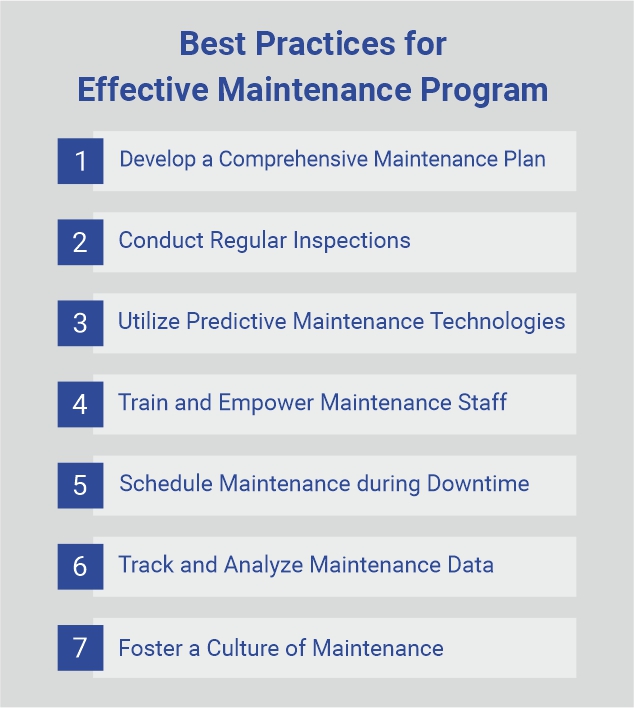
1. Ensuring Operational Efficiency
Manufacturing facilities are complex environments with numerous machines and systems working simultaneously. Regular facility maintenance ensures that these machines and systems operate efficiently, minimizing the risk of unexpected breakdowns that can disrupt production schedules. Preventive maintenance tasks, such as lubrication, calibration, and part replacements, help keep equipment in optimal condition. For instance, in a manufacturing plant, a regularly maintained conveyor belt will run smoothly, reducing the risk of production delays. This proactive approach to maintenance helps maintain a consistent workflow, which is essential for meeting production targets and deadlines.
2. Prolonging Equipment Lifespan
The machinery and equipment used in manufacturing are significant investments. Regular maintenance can extend the lifespan of these assets, providing a better return on investment. Neglecting maintenance can lead to accelerated wear and tear, resulting in costly repairs or premature replacements. For example, regular maintenance of CNC machines, such as cleaning and replacing worn-out parts, ensures their longevity and precision. This not only saves money on replacements but also ensures that the machines produce high-quality products over their extended lifespan.
3. Reducing Costs
While regular facility maintenance requires an upfront investment of time and resources, it can lead to substantial cost savings in the long run. Preventive maintenance is generally less expensive than emergency repairs, which often come with higher labour costs and parts premiums. Moreover, well-maintained equipment operates more efficiently, reducing energy consumption and associated costs. For example, a well-maintained air compressor will consume less energy and perform more reliably, leading to lower utility bills and fewer interruptions in production.
4. Ensuring Safety and Compliance
Safety is paramount in the manufacturing industry, where workers interact with heavy machinery and potentially hazardous materials. Regular maintenance helps identify and address safety hazards before they result in accidents or injuries. This proactive approach not only protects workers but also ensures compliance with safety regulations. For instance, regularly inspecting and maintaining safety systems, such as emergency shut-offs and fire suppression systems, ensures they are functioning correctly when needed. This compliance with safety standards helps avoid costly fines and legal liabilities while creating a safer work environment.
5. Improving Product Quality
The quality of manufactured products is directly linked to the condition of the machinery and equipment used in their production. Regular maintenance ensures that equipment operates at peak performance, producing consistent and high-quality products. Neglected machines can lead to defects, waste, and rework, which negatively impact product quality and profitability. For example, in the production of precision components, regularly maintained machines ensure that products meet stringent specifications and quality standards. This consistency in product quality enhances customer satisfaction and strengthens the manufacturer’s reputation.
6. Minimizing Downtime
Unplanned downtime is a significant challenge in the manufacturing industry, leading to lost productivity and revenue. Regular maintenance helps prevent unexpected equipment failures, minimizing downtime and keeping production lines running smoothly. For instance, scheduling regular maintenance during planned downtime or off-peak hours ensures that equipment is serviced without disrupting the production schedule. This strategic approach to maintenance maximizes uptime and minimizes the impact on overall productivity.
7. Supporting Sustainability and Environmental Responsibility
Sustainability is increasingly important in the manufacturing industry, with companies striving to reduce their environmental footprint. Regular maintenance plays a key role in this effort by ensuring that equipment operates efficiently and uses resources responsibly. For example, maintaining industrial HVAC systems and ensuring proper insulation can significantly reduce energy consumption and greenhouse gas emissions. Similarly, regular maintenance of water systems can prevent leaks and reduce water waste, contributing to water conservation efforts.
Implementing an Effective Maintenance Program
Given the critical importance of regular facility maintenance in the manufacturing industry, it is essential to implement an effective maintenance program. Here are some best practices to consider:
1. Develop a Comprehensive Maintenance Plan:
Create a detailed maintenance plan that outlines all the tasks to be performed, their frequency, and the responsible personnel. This plan should cover all critical equipment and systems within the facility.
2. Conduct Regular Inspections:
Regular inspections are vital for identifying potential issues before they become major problems. These inspections should be thorough and documented to ensure that nothing is overlooked.
3. Utilize Predictive Maintenance Technologies:
Leverage advanced technologies, such as IoT sensors and predictive analytics, to monitor equipment conditions in real time. Predictive maintenance helps identify potential failures before they occur, allowing for timely intervention.
4. Train and Empower Maintenance Staff:
Ensure that maintenance staff are well-trained and equipped to perform their tasks effectively. Provide ongoing training and support to keep them updated on the latest maintenance techniques and technologies.
5. Schedule Maintenance During Downtime:
Plan maintenance activities during scheduled downtime or off-peak hours to minimize disruption to production. This strategic scheduling ensures that maintenance does not interfere with normal operations.
7. Foster a Culture of Maintenance:
Promote a culture of maintenance within the organization by encouraging employees to report issues and participate in preventive maintenance activities. This collective effort helps ensure that maintenance is prioritized and performed consistently.
Conclusion
Regular maintenance is a cornerstone of effective facility management in the manufacturing industry. It ensures operational efficiency, prolongs equipment lifespan, reduces costs, enhances safety and compliance, improves product quality, minimizes downtime, and supports sustainability. By implementing a robust maintenance program, manufacturers can achieve long-term success and competitiveness in a demanding industry.
At FFServices Pvt Ltd, we understand the critical importance of regular maintenance and are committed to providing our manufacturing clients with the highest standards of facility management services. Our proactive approach to maintenance ensures that your facility operates smoothly, safely, and efficiently, allowing you to focus on what you do best – manufacturing high-quality products.
Unlock the full potential of your facility with our dedicated management solutions. Reach out to us today to take the first step towards optimized efficiency.
Industries we serve:
Automobile | Manufacturing | Pharmaceutical | Oil and Gas | Healthcare | Ancillary | FMCG | Education | Real Estate | Commercial | Mining | Hotels